DOSING AND CONVEYING OF SOLIDS IN THE CHEMICAL INDUSTRY.
Jordi Casas / Joan Jubany / Wednesday 15 February 2023
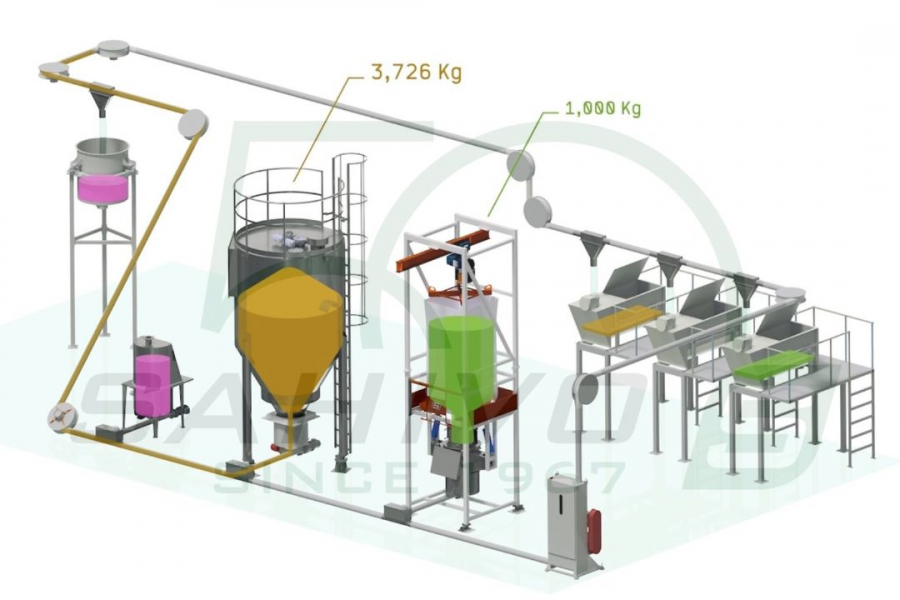
The handling, conveying and dosing powder and granular solids in the reactor and mixing tank charging in the chemical industry requires tailor-made equipment and solutions adapted to the entire plant and existing installations, compatible with Atex specifications and classified environments.
The scope of dosing solids in the chemical industry ranges from the reception of raw materials, whether from tanker trucks, Big Bag, or small sacks, to dosing at the point or points of destination. Each product to be transported and dosed deserves a previous analysis because as it is well known in the world of solid materials, appearances can be deceiving and similar products do not behave identically, just as equipment that is suitable for one application may not be valid for another.
Locating the raw material reception area in a unified area, separated from the processing plant, makes raw material management more comfortable and safer, and also allows centralization of equipment and installed power in safe and easily accessible areas, often less restrictive in terms of Atex regulations, or even in declassified areas, which is a technical and operational advantage.
In the processing area, reactors and mixing tanks are often located in ATEX classified areas (dust and/or gas), so avoiding the installation of electrical devices, motors, and filters will be an advantage in favour of optimization, safety, and ease of execution in generally limited spaces.
Regarding the product transport equipment, the advantages of the Tubular Conveyors with Chain or Cable with Disks gain competitiveness over long distances, especially:
● Facility to have different points of entry and unloading of products with the same line.
● The discharge points take up a minimum of space.
● No need for electrical power installed at the unloading points. (Only solenoid valves and sensors).
● Unloading without requiring air/product separation filters.
● Possibility to convey over long distances between loading and unloading points.
Other competitive advantages of the Tubular Disk Conveyors are the possibilities of inertisation, and their energy efficiency due to their low power consumption.
In the animation of the following link, you can see the possibilities of the Tubular Drag Conveyor system, as well as other examples with BIG BAG unloading applications and Bag Unloading Hoppers
Although long-distance pneumatic conveying systems offer good performance for the transport of solid bulk products in powder and granular form, one of their strengths is not always decisive in the chemical industry, unlike what happens in other sectors such as the food industry: the complete emptying of the pipeline, avoiding cross or bacteriological contamination in the case of working with multi-products that are not compatible with each other.
On the other hand, in the chemical industry, pneumatic conveying systems, whether in dilute phase or dense phase have certain disadvantages compared to other mechanical conveying systems, as they require air/product separation filters at the unloading point due to the generated air required for conveying, usually with venting panels with the need for ducting to a safe area.
One of SAHIVO's main values is to work together with the plant technicians, to offer global and customized solutions that adapt to the needs, valuing the different technologies and without limiting ourselves to the supply of standard equipment. Automation and process engineering will also be essential for the correct operation of the installations, for safety, the interconnection between processes, data control, limiting errors caused by the human factor, and increasing the safety of the installation and its environment.
A correct preliminary planning work, analyzing all the present and future possibilities, will lead to a satisfactory realization and running, fulfilling the expectations and providing the expected value.
Need more information?
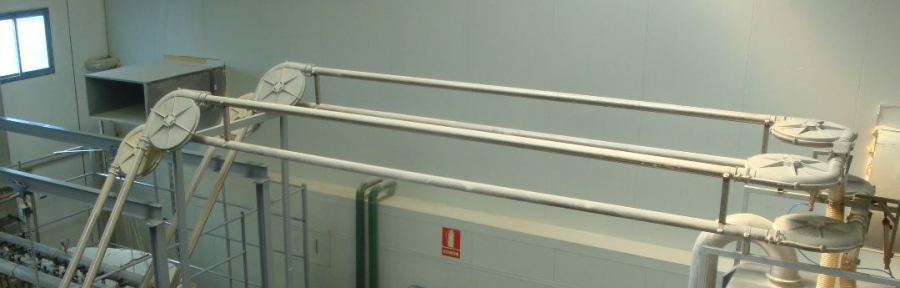